2 minute read
DISC MILL EQUIPMENT FEATURE
By Ashley Graye
So why have we been using disc mills for centuries? It's simple really, we have yet to find someting that works as well and as efficently.
Do you know where the disc mill originated from?
A small, hand operated flour mill, very similar to the ancient Buhrstone mill.
Taking a page out of the history books, disc mills rely on the exact same idea of two surfaces rotating past each other, at a set speed where only one disc is actually rotating. The distance between the two ‘discs’, or surfaces, reduces particle sizes by crushing, grinding, pulverizing, blending, cracking, refining and more.
Essentially, it’s an oversized flour hand mill, that’s not operated by hand. Instead, it’s operated by a lowpower-consumption electric motor.
Old technology, right? Well, yes, you’re right, but with leaps and bounds in terms of advancements.
First, lets look at the discs. Hundreds of years ago, the discs were all the same – made of stone, fairly flat, and the size in which the input was reduced down to relied solely on the speed of the operator, and how long they wanted to continuously crank the ‘mill’. Jump back to current day, and the discs contain a number of segments made of tungsten carbide. Sounds familiar, right? That’s because Tungsten Carbide is used to make cutting tools within the engineering industry, so saying it’s a durable material is quite the understatement. These discs in a Skiold Disc Mill can last up to 5,000 tonnes in the smallest mill, 10,000 tonnes in a midsize mill, and 20,000 tonnes in the largest mill.
How does it work, exactly?
A stationary disc is mounted inside the ‘door’ of the disc mill, which as indicated, is in a fixed position. The opposite disc which is mounted against the motor, rotates in a clockwise motion at a given speed. The distance between these two discs is adjusted according to the input and desired output size. This is easily changed by hand (using the handle on the front of the disc mill), or via the feed mill control panel (setting the actuator).

Once the desired settings are in place, the input material first passes through a segment where it’s coarsely ground between two inlet rings, then passes through the grinding discs, where it’s processed to the required size and consistency.
No matter the way in which you’re trying to reduce the particle size of your inputs, disc mills can be designed to achieve it. Shred, curl, granulate, grind, pulverize, blend, crack, cut, refine or hull, disc mills can process up to 30,000 kg/hr. Varying in sizes from industrial feed mills, all the way to on-farm feed production, disc mills are increasing in popularity. This is largely due to the previously mentioned capacity, and ability of varying the grinding degree in the midst of operation allowing the optimization of feed structure for groups of animals.
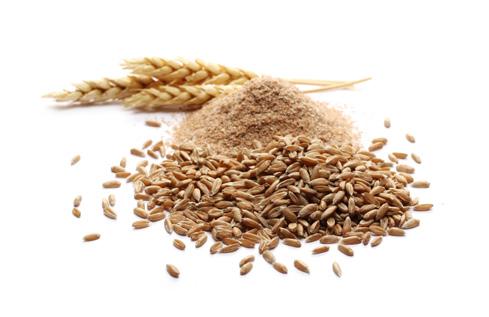

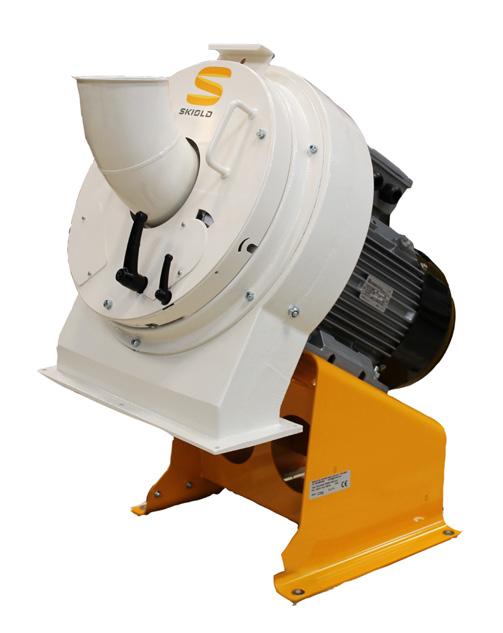
Sounds like a beast for power or energy consumption, no?
Not at all. It’s quite the opposite! Skiold disc mills consume around 5 kWh per ground tonne, when grinding wheat. Compare it to a hammer mill, and the disc mill has 25% more capacity. Additionally, the motor is mounted on the disc that rotates, allowing all of the energy produced by the motor, to be used for milling. Not only is the efficiency appealing and easy on the pocketbook, the quiet operation is easy on the ears.
So, while the technology may seem new, thousands of years of advancements have proven to be effective. Check out the leaps and bounds the technology has taken by reading more at https://westernagsystems. com/